Modular plant for filling ice cream
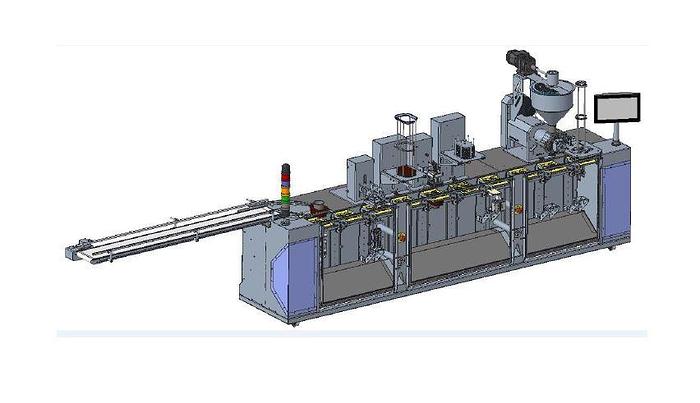
Modular plant for filling ice cream
Bad Salzuflen, Germany
Description
Formats:
Mug 120 ml to 460 ml
Output:
160 to 800 litres per hour
Dosing of dry ingredients 1 to 100 g per pack
Dosing of sauces 1 to 100 ml per pack
Stations in the line:
Cup/can dispenser
Filling station
- Must be able to handle pieces and sauces
- Must have a hopper between freezer and dosing unit with agitator
Weight monitoring
Foil sealing
Lidding station
Date station
Packing table / Packing belt
Design:
The design of the system is carried out according to food industry standards.
Special attention is paid to a high standard of hygiene, easy cleanability ("self-cleaning" by avoiding dirt corners), maintenance-friendly accessibility and functional reliability.
Container feed:
The different packs are stacked in a magazine.
A vacuum gripper (from below) separates the containers and places them in the carrier.
The filling line is currently equipped for three different containers
Ice cream filling
Volumetric dosing with a lifting piston driven by a servo motor.
A funnel with agitator is located above the slide valve.
Adding dry ingredients
The dry materials are added manually into the hopper. Optionally, this can also be done automatically at a later stage.
Checkweighing
In this station, the container is measured on a load cell.
The load cell is hermetically sealed.
Accuracy class according to OIML R60 (verifiable)
If the weight tolerance is not reached, the remaining steps on the filling line are not carried out.
Separating the film
The films are stacked in a magazine. The films are separated by vacuum grippers and placed on the packs.
The packs are fixed in position so that they do not lose their position while being moved.
Sealing films
The material fusion and sealing seam strength resulting from thermal sealing depend on several factors, including: the dwell time required for sealing, the sealing temperature and the sealing pressure.
The seal must be strong enough to withstand the rigours of transport and handling, while allowing the end customer to open the package with ease. The optimisation of the thermal seal as well as the consistent production of packaging with the appropriate seal strength are of utmost importance. Therefore, these parameters are monitored during the process and can be adjusted in the control system for each individual pack.
Place lids
The lids are stacked in a magazine. The lids are separated by vacuum grippers and placed on the packs.
In order not to lose the position during the movement of the container, it is fixed in position.
Press on lid / stamp date
The lids are now pressed onto the containers. At the same time, the date is stamped on the bottom.
The date stamp is a standard product, which is fixed on a slide.
Ejector
The finished packs are pushed onto a conveyor belt with an ejector.
Conveyor belt
The individual products are transported to the packing table on a conveyor belt.
Connection values:
Pre-fuse: 32 A CE socket approx. 10 kWh
Operating voltage: 3 L / N / PE / 400V / 50 Hz
Max. permissible deviation: + 6% / - 10
Specifications
Manufacturer | Leeotech |
Year | 2021 |
Condition | Used |
Stock Number | S10719 |